BMW (M) specialist
Passie
The Engineer’s Garage is ontstaan uit interesse voor de techniek en pure passie voor auto’s. In het bijzonder BMW M-modellen en Alpina’s. Bij ons wordt uw BMW M of Alpina met net zoveel enthousiasme onderhouden als een exclusieve Ferrari.
Engineering als basis
Door onze achtergrond in Engineering werken wij met hoge standaarden. Elke onderhouds-stap wordt nauwkeurig uitgedacht en vastgelegd.
Motorsport
Naast onderhoud en service aan straatauto’s, onderhouden wij diverse motorsport projecten voor onder andere Track Days en rally’s zoals de bekende Mille Miglia.
Over ons
The Engineer’s Garage is een service en reparatie specialist met een specialiteit in BMW M-modellen en Alpina’s. Onze onderneming is voort gekomen uit een enorme passie voor techniek.
Na het behalen van onze ingenieurs diploma’s en jaren werkzaam te zijn geweest in de Automotive en Motorsport industrie besloten wij in 2017 dat het tijd was om onze kennis en passie te bundelen en vervolgens te delen in één bedrijf: The Engineer’s Garage.
Door jarenlange werkervaring in een omgeving waar de hoogste kwaliteitseisen gelden, werken wij gestructureerder en nauwkeuriger dan gebruikelijk is bij een garage. Wij zijn ervan overtuigd dat dit de beste manier is om kwaliteit, efficiëntie en klanttevredenheid zo hoog mogelijk te houden
Autoliefhebbers in hart en nieren!
The Engineer’s Garage is ontstaan uit pure passie voor techniek en auto’s. Naast werkzaamheden voor klanten doordeweeks, werken we vaak aan onze eigen auto’s in het weekend. Hierdoor begrijpen wij als geen ander dat u alleen het beste wilt voor uw trotse bezit. Wij maken graag tijd om optimaal mee te denken over uw wensen qua onderhoud of aanpassingen aan uw auto.
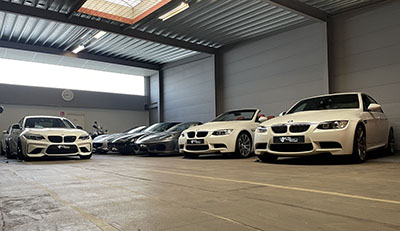